冷暖房や換気システムにおいて重要な役割を果たすダクトは、精密な板金加工によって製造されます。品質の高いダクトは建物の快適性や省エネルギー性に直結するため、適切な材料選定や製造プロセスの理解が重要です。本記事では、ダクト製造における基本知識から調達事例、コスト削減のポイントまで幅広く解説します。
Contents
ダクト調達事例
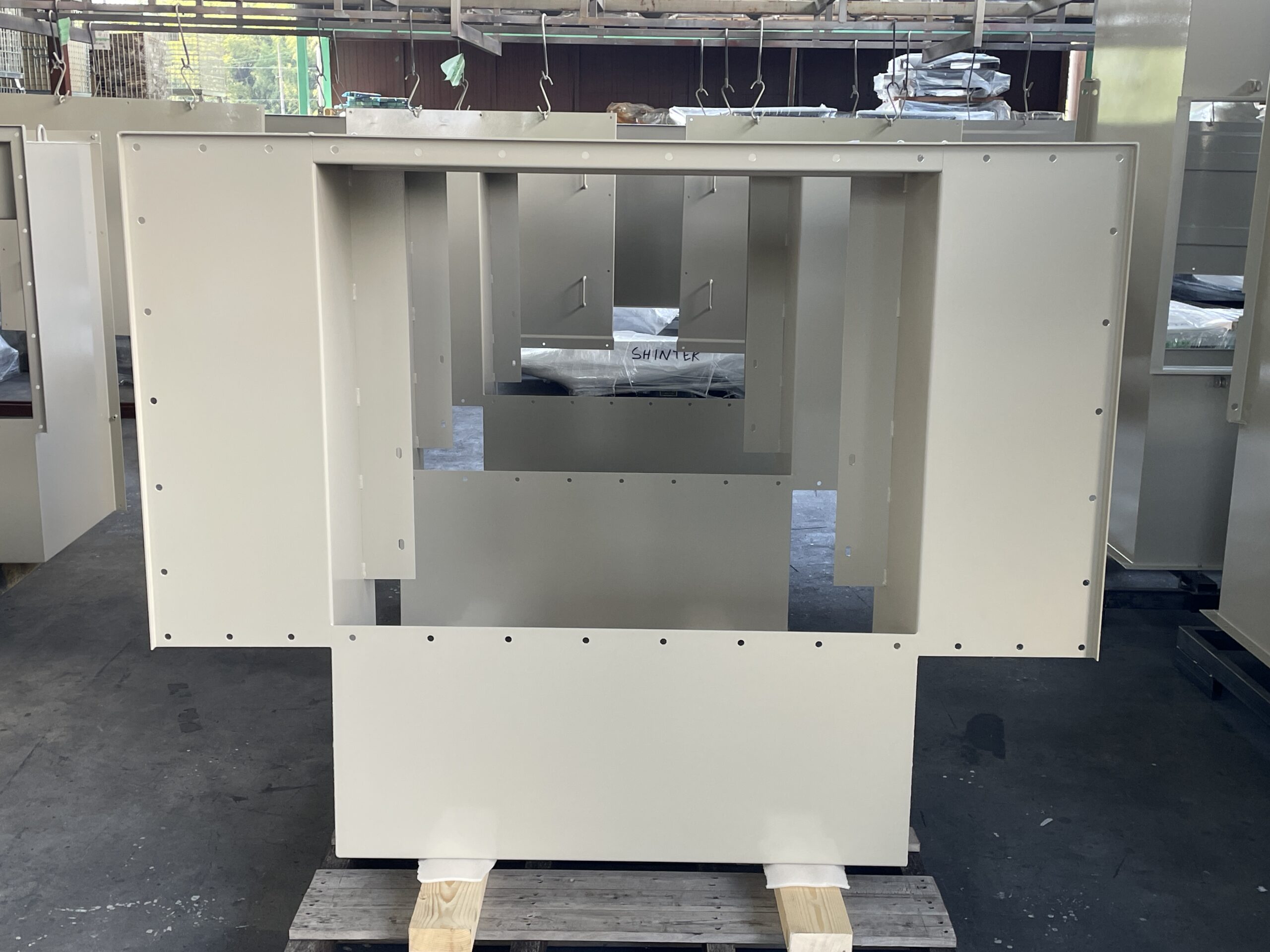
サイズ:900*340*1270(W*D*H)
材質 :SS400
特徴 :塗装込みで対応
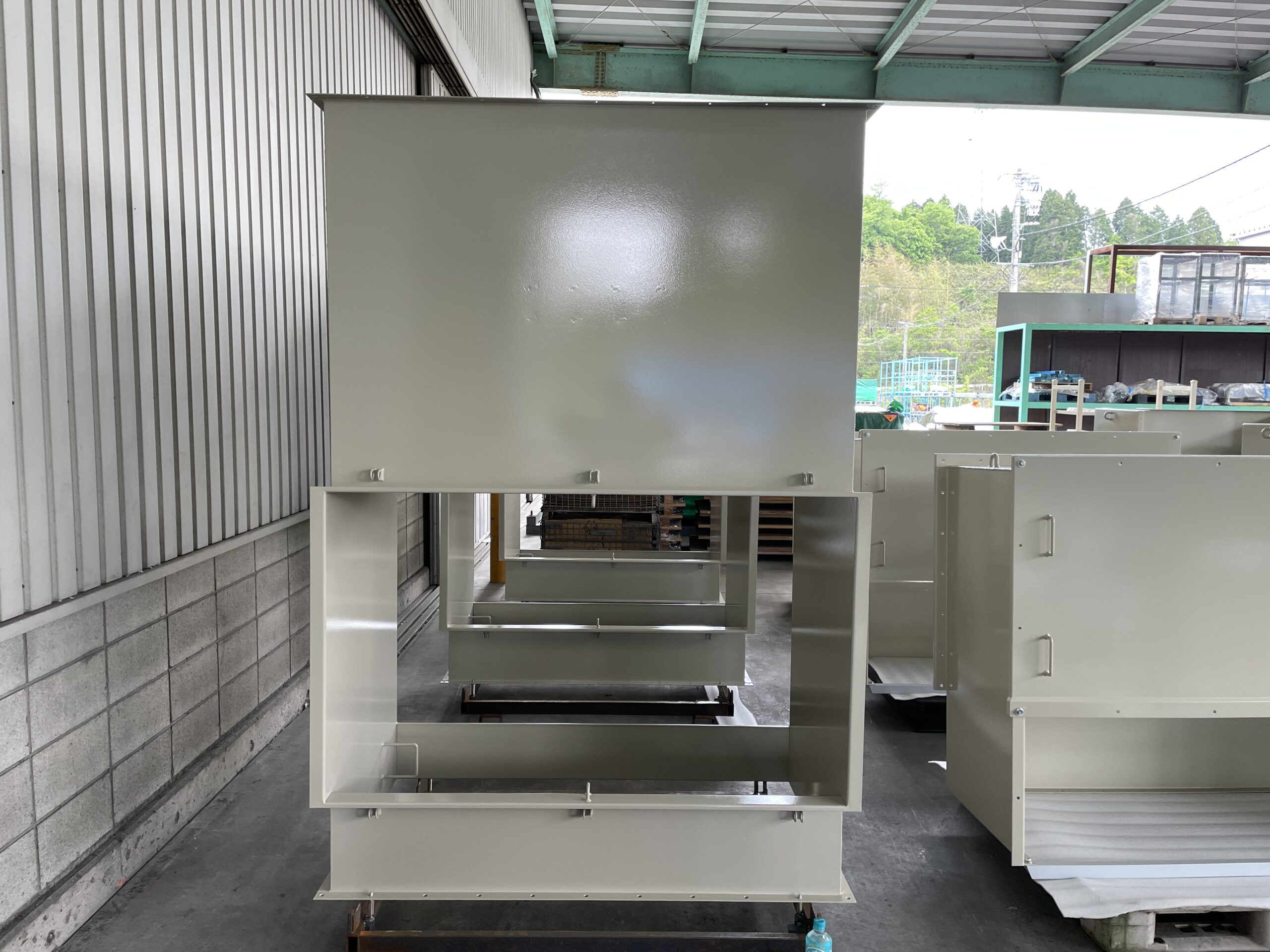
サイズ:1200*600*2600(W*D*H)
材質 :SS400
特徴 :塗装込みで対応
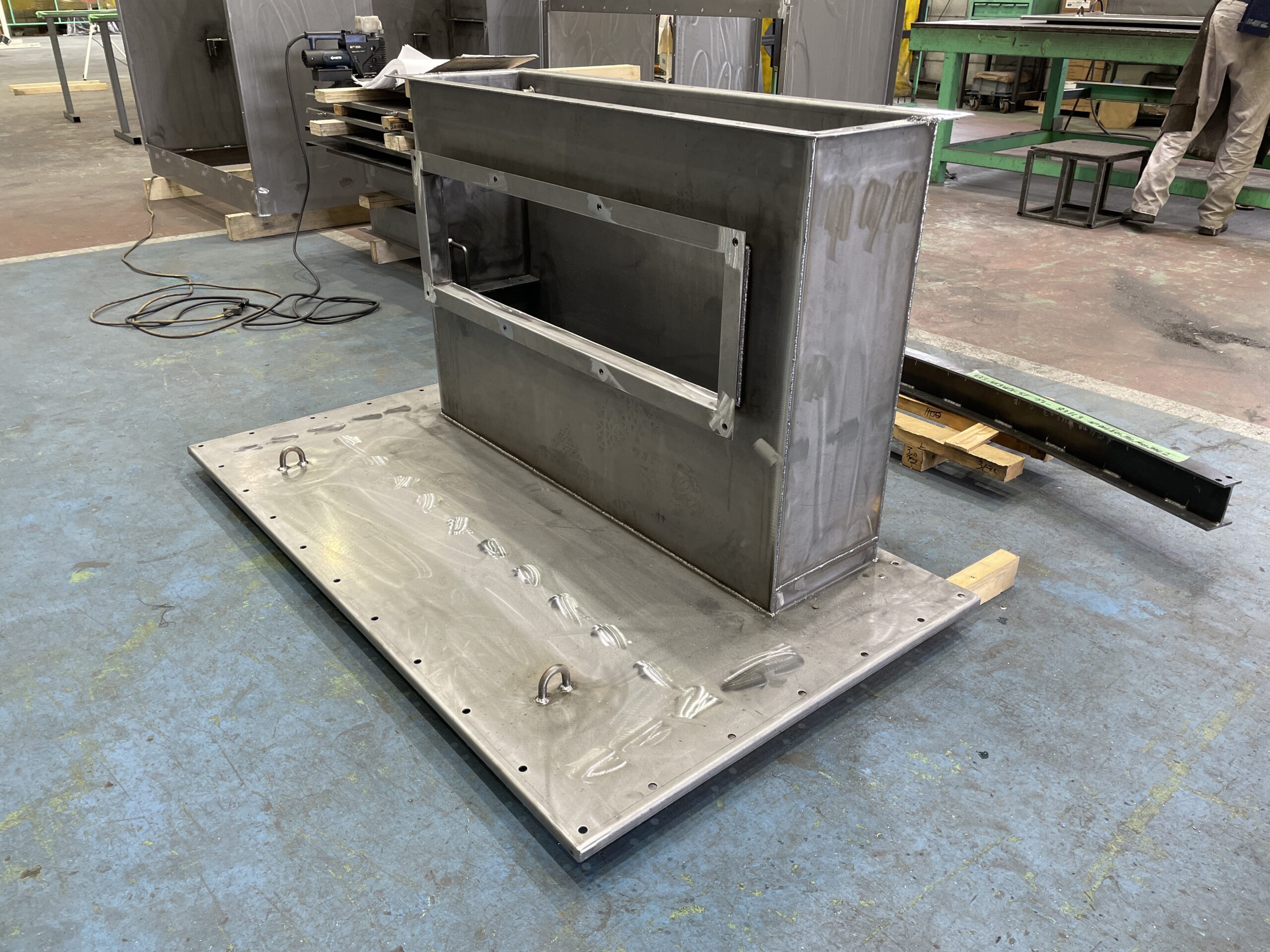
サイズ:1500*1000*800(W*D*H)
材質 :SS400
特徴 :塗装込みで対応
調達コストを下げる取り組み
当社ではダクトをはじめとした板金筐体品の調達を支援させていただく中で、材質や工法の見直しなどを行うことによって多くのコストダウンを実現してきました。
- 設計条件の再検討(仕様、サイズ、寸法公差など)
板金加工においては素材の切り出し方一つでも無駄が生じることがあります。原板のサイズや厚みに合わせた設計を考慮することが重要となります。また、加工のしやすさを踏まえた仕様検討も欠かせません。過度に複雑な形状や厳しすぎる寸法公差は製造コストを押し上げる要因となるため、機能を損なわない範囲での簡素化を検討することでコスト調整を図る場合もございます。 - 加工範囲の見直し
こちらも効果的なアプローチです。製造工程の一部を外部委託し、残りを自社で対応するなど、工程の分担を最適化することでコスト削減につながるケースがあります。もちろん外部委託を実施する際には委託先の技術レベルや材料調達コストなども考慮しなければならず、これら要素を総合的に判断する必要がでてきます。
ゴール(最終製品の出来上がりや機能)は同じであっても、その製造方法には複数の選択肢が存在します。コストや納期などの要件を踏まえながら、最適な製造アプローチを検討することが板金部品調達においては欠かせません。
ダクト製造の基礎知識
一般的に使用される材料
ダクト製造には主に以下の材料が使用されます。
- SPHC(熱間圧延軟鋼板):強度と加工性のバランスが良い一般的な素材
- 亜鉛メッキ鉄板:防錆性に優れ、一般空調向けに広く使用される
- ステンレス鋼板:高い耐腐食性が必要な環境や食品・医療施設向け
これらの材料は用途や環境条件に応じて選定され、ダクトの耐久性や性能に大きく影響します。
加工プロセス
ダクト製造の主なプロセスは次のとおりです。
- 切断:レーザーカットやパンチングマシンを使用して、図面に基づいた精密な切断を行います。
- 曲げ加工:プレス機やベンダー機を利用して板金を立体形状に成形します。
- 溶接:各パーツを接合し、強度を確保します。
- 表面処理:必要に応じて塗装やメッキ処理を施し、耐腐食性や意匠性を向上させます。
- 組立・検査:各部品を組み立て、寸法確認や漏れチェックなどの品質検査を実施します。
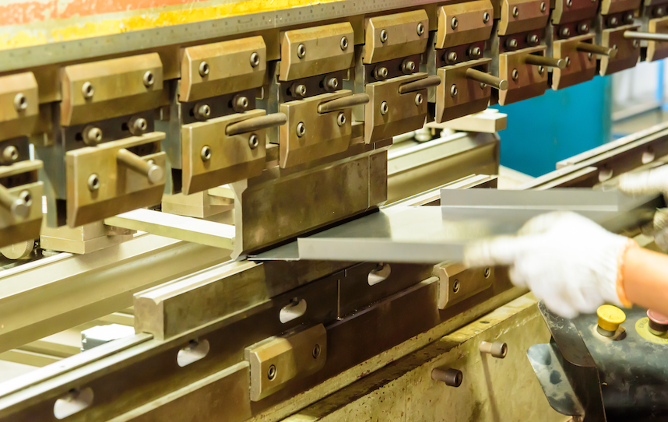
環境条件に応じたダクト素材の選定基準
ダクトの使用環境は設置場所や用途によって大きく異なります。環境条件に応じた素材選定が、ダクトの寿命やパフォーマンスを左右します。
耐腐食性の考慮
化学工業や食品産業など腐食性物質が存在する環境では、耐腐食性の高いステンレス鋼や特殊コーティングを施した素材が推奨されます。これによりダクト内の流体汚染リスクを低減し、長期的なメンテナンスコストの削減にもつながります。
温度・圧力条件への対応
高温または高圧環境では、材料の熱的・機械的特性が重要です。
- 高温環境:熱変形に強いステンレス鋼やアルミニウム合金
- 高圧環境:適切な厚みを持つ鋼板や補強構造を備えたダクト
内部環境の清浄性
医療機関や食品製造施設では、内部表面の清浄性維持が不可欠です。内部表面が滑らかで汚れが付着しにくい素材や、抗菌性を持つ特殊コーティング処理が施された材料が選ばれることが多いです。
設置環境に応じた考慮点
- 軽量性:天井設置など重量制限がある場所ではアルミニウム製が適しています
- 可動性:頻繁な移動や変更が必要な場合は、フレキシブルダクトなど柔軟性のある素材が有効です
- 屋外環境:紫外線や風雨にさらされる場所では、耐候性に優れた材料や表面処理が必要です
流体力学を考慮したダクト設計
ダクトの性能は流体力学の原理に基づいた設計によって大きく左右されます。効率的な空気流通を実現するためには、以下の要素を考慮する必要があります。
ベルヌーイの定理と連続の式
ベルヌーイの定理によれば、流速が増加すると圧力は低下します。この原理はダクト設計において断面積の変化を考慮する際に重要です。また、連続の式に基づき、断面積が変わると流速も変化することを考慮した設計が必要となります。
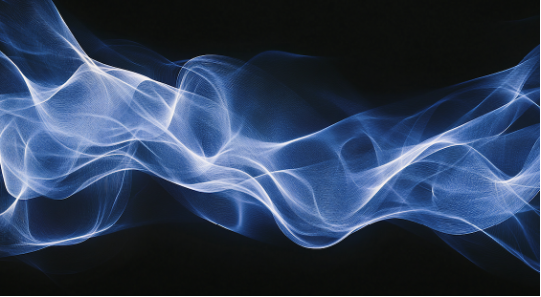
摩擦損失と圧力損失の最小化
ダクト内の摩擦は流体抵抗を生じさせ、圧力損失の原因となります。これを最小限に抑えるためには以下の考慮が必要です。
- 滑らかな内部表面仕上げ
- 最適な断面形状の選定
- 急激な方向変化の回避
これらの対策により、エネルギー効率の向上とランニングコストの削減が可能になります。
最適な形状設計
曲がり部分や分岐部は流れが乱れやすく、効率低下の原因となります。滑らかな曲線や適切な接続方法を採用することで、これらの問題を軽減できます。
- エルボ(曲がり部分)の適切な曲率半径
- 分岐部における流れの分配の最適化
- 断面積の急激な変化の回避
大型ダクトの品質チェックポイント
大型ダクトでは特に、製造品質が性能や安全性に直結します。重要な品質チェックポイントは以下の通りです。
材料検査と寸法精度
- 使用材料の規格適合性確認
- 板厚の均一性検査
- 加工寸法の精度確認(レーザー測定器などを活用)
ダクトの材料は、その耐久性や性能に大きな影響を与えます。一般的に、軽量で強度があり、耐腐食性のある材料が求められます。また、加工されたダクトの寸法精度は、設置時のフィット感に影響します。誤差が大きいと、気密性が損なわれ、エネルギー効率が低下する恐れがあります。したがって、加工時の寸法誤差の管理が重要です。
接合部の品質確認
- 溶接部の強度と均一性
- リベット接続部分の固定状態
- 断熱材の適切な配置と固定
溶接やリベット接続部分は、漏れや強度不足の原因になるため、検査が欠かせません。断熱材の配置と接続部分の確認も重要です。
気密性と耐圧性のテスト
- 圧力試験による漏れ検査
- リークチェック(ヘリウム漏れ試験や水圧試験)
- 風洞試験(必要に応じて)
完成したダクトが適切な圧力に耐えられるかを確認するために、圧力試験を行います。これは、漏れがないことを確認する上で非常に重要なテストです。追加的に、風洞試験を行う場合もあります。
表面処理の品質確認
- コーティングの均一性
- 塗装膜厚の確認
- 耐食性テスト(特に腐食環境で使用される場合)
ダクトの表面処理は、耐久性と見た目を向上させます。腐食防止や摩耗防止のための塗装やコーティングが施されているかを確認することが必要です。特に屋外に設置されるダクトは、これらの処理が必須です。
ダクトの調達はTOHMAへお任せください
当社ではダクトをはじめとした大型板金筐体の調達を承っております。縦横高さ2m以上の製品も取り扱い可能で、塗装・表面処理や電子部品・制御盤配線の組み込みも一貫して対応いたします。
調達を依頼いただくことでコストややり取りが増えることを懸念される方もいらっしゃいますが、工法の見直しや製図等の生産工程の一部を弊社で負担することで、転注検討でご相談いただいたお客様の約9割が同程度の取引価格、もしくはコストダウンを実現しております。
製造業界経験10年以上の担当者がスピーディーに対応いたしますので安心してお任せください。