Contents
鋳物製キャスターの特徴
鋳物によるキャスターは、重荷重への対応や耐摩耗性の高さなど、優れた性能を発揮することから、多くの産業分野で重宝されています。鋳鉄やダクタイル鋳鉄(球状黒鉛鋳鉄)をはじめ、さまざまな合金の特性を活かして製造される鋳物製キャスターは、量産品から特殊仕様まで幅広いニーズに応えることが可能です。
鋳物製キャスターは、基本的な円筒形の車輪だけでなく、リムの形状や幅、肉厚、スポーク構造などをカスタムできる柔軟性が大きな魅力です。たとえば、高い荷重に対応しながら軽量化したい場合、リムに肉抜きのスポーク状デザインを取り入れることがあります。また、公共施設で使用する大型のカートや台車用には、静粛性を保つために外周にゴムや樹脂を組み合わせる複合構造にするケースも。
鋳物は溶けた金属を型に流し込む製法ゆえ、形状の自由度が高いことから、機能性だけでなくデザイン性を重視したキャスターを生み出すことも可能です。
基本構造
鋳物製キャスターは、ハブ(車軸部分)とリム(外周部分)を一体化した形状が多く、車輪のコア部分を鋳物で成形する点が特徴です。特に重荷重用では、鉄製ホイールが必須となり、ゴムやウレタンなどのタイヤ材を被せない「オールメタル構造」も珍しくありません。使用目的に応じて、表面に樹脂やゴムを張り付ける場合もありますが、コア自体を頑丈に作ることで、一度の投資で長期間使用できるというメリットをもたらします。
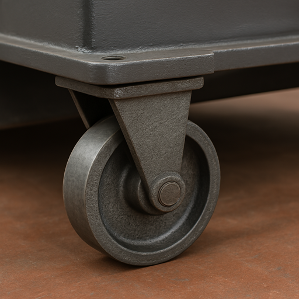
鋳造工程の流れ
金型・砂型の製作
鋳物製キャスターの製造では、まずは成形用の型(パターン)が必要です。量産向けには金属製の金型を使い、少量多品種や試作段階では砂型を使うこともあります。金型は高コストですが、高精度かつ量産に適しており、鋳放し状態での仕上げ精度が高いのが利点です。一方、砂型は製作コストを抑えられるため、大型キャスターや特殊形状の試作などに用いられます。
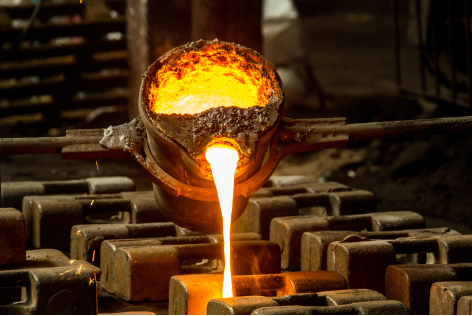
溶解・湯流し
型が用意できたら、炉(電気炉やキュポラ炉など)で鉄や合金を溶解し、溶けた金属を湯口から型の中に流し込む「湯流し」を行います。鉄の溶解温度は約1,400~1,500℃にも達し、温度管理を誤ると強度不足や巣(す)が発生しやすくなるため、厳格な温度・成分管理が欠かせません。キャスターは一定の肉厚が必要ですが、厚すぎると凝固不良を招くリスクがあるため、流路設計や放熱シミュレーションを入念に行います。
冷却・型ばらし
湯流し後、金属が固まるまで適切に冷却し、型をばらして鋳造品を取り出します。砂型を使う場合は、振動や打撃で砂を落としながら製品を取り出す「シェイクアウト」が行われ、後続の清掃工程で残存する砂を取り除いていきます。この時点で大まかなキャスターの形状ができあがっているものの、バリや湯口跡などが残っているため、後述する仕上げ工程に進みます。
キャスターに適した材質は?
キャスターに用いられる鋳物素材は、大きく分けてねずみ鋳鉄(FC)やダクタイル鋳鉄(FCD)が主流です。ねずみ鋳鉄は、一般的な鋳鉄よりも加工がしやすく、コストも比較的安価なため多用されます。一方、ダクタイル鋳鉄は球状黒鉛を含む組織によって強靱性が高く、衝撃や曲げ荷重に対してもより強度を発揮します。重荷重向けや高い耐久性を求められる場合は、ダクタイルが選択されることが多いです。
場合によっては、ステンレス系合金や特殊鋼を用いるケースもあり、耐熱性や耐食性を重視する現場で採用されることがあります。たとえば食品工場や化学プラントなど、サビの発生を許容できない環境ではステンレス鋳物が選択肢に入りますが、コスト面では一般的な鋳鉄よりも高くなるため、導入前のメリット・デメリット評価が必須です。
鋳物製キャスターに問われる強度と耐久性
鋳物製キャスターの大きな特長として、焼入れなどの熱処理によって局部的に硬度や耐摩耗性を高めることができる点が挙げられます。たとえば、ホイールのリム部分や車軸接触面など、摩擦や衝撃が集中しやすい箇所を選択的に焼入れすることで、全体重量を増やすことなく耐久性を強化できます。
熱処理には焼入れ以外にも、焼戻しや高温・低温の応力除去など様々な方法があり、材料や仕様に応じてベストな組み合わせを選択します。適切な熱処理を施すことで、キャスター全体としてバランスのよい強度・硬さを得られると同時に、長期使用による摩耗や変形を最小限に抑えられます。
鋳物製キャスター精度を左右させる機械加工と最終仕上げ
鋳造品は、取り出した直後はバリや湯口跡、巣などがあるため、そのままの状態ではキャスターとして使用できません。そこで行われるのが機械加工(旋盤加工・フライス加工など)と、バリ取りや面取りなどの仕上げ工程です。
旋盤加工
ホイール部分が円形状であることから、車輪の外周面や軸穴の同心度を高精度で確保するために旋盤加工が多用されます。ここで求心度をしっかり出すことで、回転ブレや騒音、偏摩耗を抑えられます。
フライス加工
ストップ機構やブレーキユニットを取り付ける際に必要な穴あけや平面切削を行い、組み立て精度を高めます。
仕上げ・バリ取り
隅々に残るバリや鋳造時に発生した小さな欠陥を除去し、スムーズな回転と安全性を実現します。
最終段階では、表面処理(塗装やメッキ)を行うこともあり、用途に合わせてサビ止めや光沢仕上げなどを選ぶケースも多いです。
安心して利用するための品質管理
重荷重に耐え、高い回転性能と長寿命が求められる鋳物製キャスターでは、製造後の品質保証が欠かせません。具体的には、以下のような検査工程が挙げられます。
- 外観検査
バリやクラック、鋳造欠陥(巣・ヒケ)などの有無を目視や非破壊検査装置で確認し、表面の均一性をチェックします。 - 寸法測定
軸穴径、ホイールの外径や厚みなど、設計図通りの寸法精度が確保されているかを測定器で検証します。回転バランスなども確かめ、振れや偏りがないかを評価します。 - 硬度測定・強度試験
熱処理後の硬度や、荷重をかけた際の変形量を調べることで、想定された負荷条件に耐えられるかを判断します。必要に応じて、破壊試験や疲労試験を行うこともあります。 - 組み付け検査
キャスター本体と軸受け、ブレーキユニットなどを組み合わせた際に、スムーズに回転するか、ロック機構が正常に作動するかなどをチェックします。
これらの厳格な検査工程をクリアすることで、安心して鋳物製キャスターを導入し、長期にわたって使用することが可能です。
キャスター調達はTOHMAへお任せください
当社ではキャスターをはじめとした鋳造品の調達を承っております。また、小・中型部品だけでなく大型鋳造品(500⾓‧ φ300以上)の取り扱いも可能で、塗装・表面処理も一貫して対応いたします。
調達を依頼いただくことでコストややり取りが増えることを懸念される方もいらっしゃいますが、工法の見直しや製図等の生産工程の一部を弊社で負担することで、転注検討でご相談いただいたお客様の約9割が同程度の取引価格、もしくはコストダウンを実現しております。
製造業界経験10年以上の担当者がスピーディーに対応いたしますので安心してお任せください。