Contents
切断機における筐体の役割
切断機は、金属や樹脂、木材など、多様な材料を素早く正確に切断するための産業用機械です。レーザー切断機やプラズマ切断機、バンドソーなど、加工方式はさまざまですが、高速回転する刃や強力なエネルギーを扱うという点はいずれも共通しており、安全性と防塵・排気対策が非常に重視されます。こうした切断機の性能を支え、作業者を保護し、切断時に生じる粉塵や熱・火花を適切に処理するために欠かせないのが、板金加工を用いた筐体の存在です。
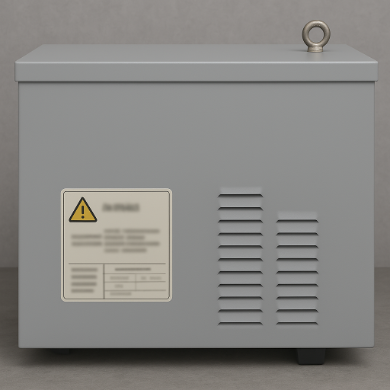
切断機の板金筐体設計
切断機は、高速で刃物が動作したり、レーザー光やプラズマアークといった強力なエネルギーを発生させたりするため、作業者を危険から守り、周囲環境を清潔に保つための筐体設計が必須となります。具体的には、以下の検討が必要です。
1. 安全性の確保
作業者が誤って手や工具を入れないよう、適切な遮蔽構造やドアのインターロック機能などを設け、危険を未然に防ぎます。また、火花や切断屑が飛散しないようにするため、筐体全体に十分な強度を持たせるとともに、隙間を最小限に抑える設計が重要です。
2. 防塵・排気機能
切断作業では金属粉や樹脂粉、煙が大量に発生します。これらが機械内部や作業場に充満すると、故障や作業ミスのリスクが高まるため、適切な排気・換気構造とフィルタリングシステムを備え、筐体内部および周辺環境をクリーンに保つ必要があります。
3. 操作性・メンテナンス性
作業者がスムーズに切断作業を行えるよう、操作パネルやモニターを見やすい位置に配置し、刃やレーザーユニットの交換・調整が簡単に行えるように、大きく開口できるドアや点検口を設けることが望まれます。
4. 振動・騒音対策
切断時の衝撃や騒音を軽減するため、筐体に補強リブや防振材を適切に配置し、不要な振動や共振を抑えることが、安定した切断精度と作業者の快適性につながります。
切断機の筐体に求められる仕様
高剛性・強度
切断作業はモーターや刃、レーザーユニットなどの駆動部に負荷がかかり、振動が発生しやすい環境で進められます。筐体の強度不足は、切断精度の低下や騒音、故障リスクにつながります。そこで、板厚や溶接方法を厳密に検討しながら、強度と剛性を両立する設計が欠かせません。
- 溶接ビードの歪みを最小限に抑える工夫
- リブ(補強材)の配置と適切な溶接順序
- 必要に応じた複数材質の組み合わせ
これらを組み合わせることで、耐久性と剛性の高い筐体を実現します。
防塵・排気機構
切断作業時に発生する粉塵や煙を効率よく排出するため、排気ダクトやファンの容量、配管径などを事前に検討しなければなりません。場合によっては、フィルタを組み込んで回収効率を高める工夫も必要です。特にレーザー切断やプラズマ切断では、高温・高速で材料を溶融するため、微細な金属粉が大量に舞うことがあります。
- ダクトレイアウトを短く・シンプルにして排気効率を高める
- 防火ダンパーや耐熱素材の採用
- 定期的にフィルタ交換が行えるよう、点検口を設ける
これらを組み込んでおくと、切断機本体や周辺機器へのダメージを抑え、長期的な安定稼働を実現できます。
メンテナンス性
切断機の稼働状況を常に良好に保つには、消耗部品の交換や定期的な清掃が欠かせません。メンテナンスを容易にするため、筐体のドアや点検口の大きさ・位置に配慮し、主要な部品にアクセスしやすい設計を行います。各種ケーブルの通線ルートを整頓しやすくし、取り外しが必要な際も作業時間を短縮できるようにすることが理想です。
製造プロセスにおける板金加工のポイント
切断機の筐体製造においては、設計・部品加工・溶接・仕上げ・塗装・組み立て・最終検査という大まかな流れがあり、そのなかでも板金加工と溶接の品質は最終製品の性能を大きく左右します。以下では、各工程で特に気を配るべきポイントを取り上げます。
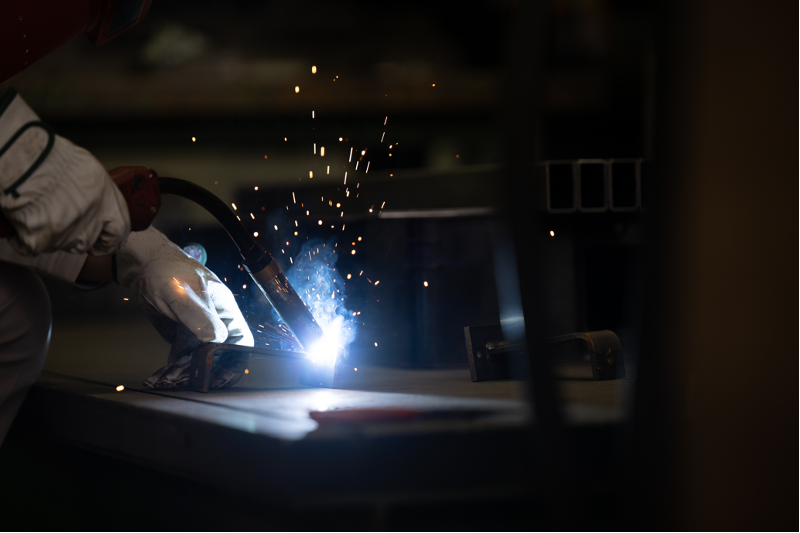
1. 設計段階での加工性・強度シミュレーション
筐体の形状や大きさ、リブ(補強材)の配置は、部品加工や溶接のしやすさに直結します。CADソフトによる3Dモデリングの段階で、曲げ加工の展開図をイメージしやすいようパーツを分割したり、レーザー切断機で切り出す際の歩留まりを考慮することが肝心です。
また、高剛性が求められる箇所と、人が操作するために開閉や取り外しが多い箇所では、板厚を変えたり、異なる材質を組み合わせることで最適化を図ります。設計段階で強度シミュレーションを行うことで、溶接や組み立て後に発生する歪みや振動の問題を事前に把握し、補強方法やリブ設計の最適案を導き出すことが可能です。
2. 部品加工(レーザー切断やプレスブレーキなど)
設計図面に基づき、レーザー切断機やタレットパンチプレス、プレスブレーキなどを駆使して板金部品を製作します。特に切断機の筐体は、操作パネル用の穴あけやドアの開口部、配線用のケーブル貫通口など、複雑な加工が多岐にわたるため、切断や曲げの精度が仕上がりを左右します。
- レーザー切断機による部品切り出し
厚板から薄板まで安定した切断精度が得られ、微細な形状も再現性が高いのが利点です。 - プレスブレーキによる曲げ加工
切断後の平板を設計通りの角度で曲げる際、弾性復元量(スプリングバック)を考慮し、補正値を設定します。切断機筐体は大きなサイズになる場合も多く、曲げ加工中の部材保持やアライメントがずれないよう丁寧な治具設計が必要です。 - 開口や小穴の加工精度
センサーや操作パネルを取り付ける穴は、誤差があると取り付け不可や水・粉塵の浸入リスクを高める原因となります。公差範囲を厳格に管理し、後工程での手直しを最小限に抑えるよう注意します。
3. 組み立て・仮付け溶接
部品が完成したら、仮付け溶接で全体の形状を組み上げていきます。切断機の筐体は箱型構造が多く、外周部に複数のパネルを組み合わせるため、寸法の狂いが累積しやすいのが難点です。そこで、部品同士の合わせ面がきちんと合うよう、専用の治具や位置決めピンを使って組み立て精度を向上させます。
仮付けの段階で、ドアの開閉具合やインターロックスイッチの取り付け位置、内部の仕切り板や補強材の配置を確認し、問題があれば微調整を行うのがポイントです。切断機は安全性や防塵性が要求されるため、ドアと筐体本体の密閉度合いを試し、気密性や排気の流れを想定しておく必要があります。
4. 本付け溶接と歪み対策
仮付けを終えたら、徐々に本付け溶接を進めます。溶接作業では、局所的な熱がかかるため、板金部品が歪んで寸法に狂いが生じることがあります。この歪み対策として、溶接順序を最適化して熱の集中を避けたり、対角線上で溶接を行いながら徐々に進める方法が一般的です。
切断機の筐体は、ドアやカバーの隙間が少しでもずれると、防塵や安全性に問題が出ることも少なくありません。そこで、要所要所で溶接ビードを施すたびに寸法を計測し、必要に応じて修正を加えるステップが欠かせません。特に大型筐体では、部分ごとにバイスやクランプを使用して歪みを抑えるのも効果的です。
5. バリ取り・研磨と仕上げ処理
本付け溶接が完了した段階で、溶接ビード周りやエッジ部分に生じたバリやスパッタの除去を行います。切断機の筐体は、エッジやコーナー部に触れる頻度が高い箇所が多く、バリが残っているとケガやトラブルの原因になります。
また、外観を重視する箇所やドアの合わせ面などは、研磨作業によって段差や傷を目立ちにくくする仕上げを行います。塗装前処理(酸洗い・リン酸亜鉛処理など)をしっかりと行うことで、塗膜の密着性を高め、腐食や剥がれを防止します。
6. 塗装・表面処理
塗装や表面処理は、筐体の耐久性と意匠性を決定づける重要工程です。切断機の筐体は、粉塵や油、熱など過酷な条件にさらされやすいため、厚膜塗装や粉体塗装など、耐摩耗性・耐薬品性に優れた手法が選ばれることが多いです。
また、耐候性が求められる環境では、亜鉛メッキや合金メッキ処理をした鋼板を下地に使うなど、複数の表面処理を組み合わせる場合もあります。いずれにしても、前処理の段階でしっかりとバリや油分を落とし、表面を滑らかに整えることで、長期間にわたり美しさと耐久性を保つ塗装を実現します。
7. 最終組み立て・検査
塗装が完了したパーツを組み上げ、ドアやパネルを取り付け、インターロックやセーフティスイッチの配線を施すのが最終組み立て工程です。排気ファンや集塵装置の動作確認、排気ダクトの気流測定などもこの段階で行い、切断機特有の防塵・防火対策が正しく機能するかをチェックします。
最後に、外観の傷や塗装ムラ、ドアの密閉度合い、操作パネルの位置精度などを総合的に検査し、不具合があれば即座に修正して出荷準備に入ります。こうしたきめ細かなチェックを積み重ねることが、切断機の筐体としての完成度と信頼性を高める要になります。
切断機の筐体製造はTOHMAへお任せください
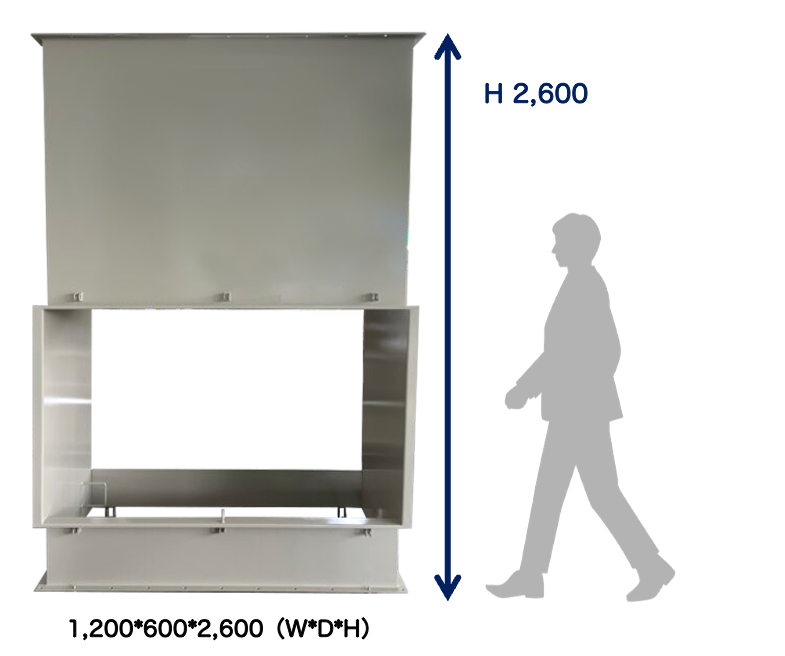
当社では切断機用の筐体をはじめとし、2m以上の中〜大型筐体板金品の調達を得意としております。塗装や、筐体内の電子部品・配線等の組み込みも一貫して対応いたします。
調達を依頼いただくことでコストややり取りが増えることを懸念される方もいらっしゃいますが、工法の見直しや製図等の生産工程の一部を弊社で負担することで、転注検討でご相談いただいたお客様の約9割が同程度の取引価格、もしくはコストダウンを実現しております。
製造業界経験10年以上の担当者がスピーディーに対応いたしますので安心してお任せください。