フランジ加工は産業界において重要な製造工程の一つであり、特に鋳造によるフランジ製造は効率的かつ量産に適した方法として広く用いられています。フランジ加工の基本概念から鋳造によるフランジ製造の詳細までを体系的に解説します。
Contents
フランジの基本
フランジとは、配管や機械部品を接続するために端部に取り付けられる円形または矩形の部品を指します。一般的にボルトや溶接による固定が可能であり、接続性の向上や密閉性の確保を目的とします。
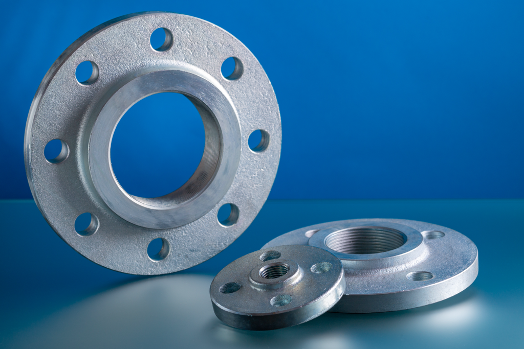
フランジの機能と特徴
フランジの主な機能は以下の通りです。
- 接続性の向上: 異なる部品同士を効果的に接合できます
- シール性: 特に配管システムにおいて流体の漏れを防止します
- 構造的強度: 接合部の強度を高め、安定した構造を実現します
- メンテナンス性: ボルト締結型のフランジは、メンテナンスのための着脱が容易です
フランジの形状は用途に応じて多様化しており、円形や矩形など様々なデザインが存在します。また、使用環境や目的によって最適な形状が選択されます。
フランジの種類と用途
接合方式による分類
スリップオンフランジ(差込み溶接式)
パイプを差し込む形で接続する一般的なタイプ
施工が容易だが、高温配管には適さない場合がある
ウェルドネックフランジ(突合せ溶接式)
長い首部を持ち、理想的な溶接接合を実現
高圧・高温環境に適しており、流体の流れを妨げない
ねじ込みフランジ
ネジによる接合が可能で、取り外しが容易
メンテナンス性に優れるが、シール性は溶接式に劣る
ルーズフランジ(遊合型)
スタブエンドと組み合わせて使用
自由に回転できるため、ボルト位置の調整が可能
産業別による分類
フランジは多くの産業分野で幅広く活用されています。
建設業: 大型構造物の接合部
石油・化学産業: 高圧・高温環境での配管接続
水処理施設: 大口径の配管システム
食品産業: 衛生的な接続が求められる配管
自動車産業: エンジン部品やエキゾーストシステム
フランジの規格と品質管理
フランジの製造には各種規格が存在し、品質管理の基準となっています。
主な規格
- JIS B 2220:日本の鋼製管フランジの規格
- ANSI/ASME B16.5:米国の配管用フランジ規格
- DIN:ドイツ工業規格におけるフランジ規格
- ISO:国際標準化機構のフランジ規格
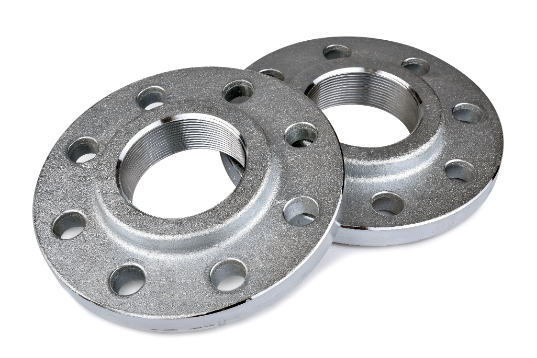
鋳造によるフランジ製造
鋳造は、溶融した金属を型に流し込み冷却・固化させることで所望の形状を得る加工法です。鋳造によるフランジ製造のメリットは、複雑な形状の再現性が高く、大量生産に適している点にあります。
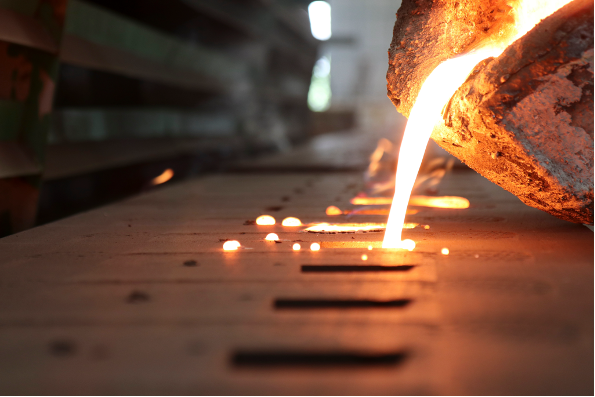
鋳造フランジの製造工程
①材料選定
鋳造フランジの材料には、用途に応じて様々な選択肢があります。
鋳鉄…コストパフォーマンスが高く、優れた鋳造特性を持つが、鋳造欠陥が発生しやすい
※球状黒鉛鋳鉄(ダクタイル鋳鉄)など、一部素材は耐久性が高く、鋳造欠陥のリスクが抑えられることも。
鋳鋼…高い強度と耐久性を持つが、製造コストが比較的高い傾向にあります。小ロットや特殊用途よりも、量産時にメリットを発揮
その他…アルミニウム合金やステンレス鋼なども用途に応じて使用される
②型の製作
フランジ形状に合わせた鋳型の製作は、製品品質に直結する重要な工程です。
砂型鋳造:一般的な方法で、木型から砂型を作成
金型鋳造:精度が高く、量産に適している
消失模型鋳造:複雑な内部形状を持つフランジに適している
③鋳造工程
実際の鋳造工程は以下のステップで進行します。

- 金属の溶解:原材料を溶解炉で高温に加熱し溶融状態にする
- 型への注湯:溶融金属を鋳型に流し込む
- 冷却と凝固:適切な冷却条件で金属を固化させる
- 型抜き:凝固後、鋳型から製品を取り出す
④後処理加工
鋳造後のフランジは、以下の後処理を経て完成品となります。
バリ取り:余分な部分の除去
機械加工:接合面や穴の精密加工
熱処理:必要に応じて強度向上や応力除去のための処理
表面処理:耐食性向上のための処理(めっきや塗装など)
⑤検査・試験
完成したフランジは品質保証のため、以下の検査が実施されます。
寸法検査:規格との適合性確認
非破壊検査:内部欠陥の検出(X線検査や超音波検査など)
耐圧試験:使用環境を想定した性能確認
材質分析:化学組成や機械的特性の確認
鋳造フランジの特性と利点
鋳造フランジにおいては、他の製造方法と比較して生産コストが抑えられるという経済的なメリットがあります。
また、複雑な形状も比較的容易に製造できるため、設計の自由度が高いという特徴が見られます。同一形状の製品を効率よく生産できるため、大量生産に適しており、型の修正により比較的容易に設計変更に対応できる柔軟性があります。加えて、サイズのフランジを同様の工程で製造できるため、サイズ調整も容易に行えます。このように鋳造によるフランジ加工は様々な利点があります。
鋳造フランジの課題と対策
一方で鋳造フランジ製造には注意すべき課題もいくつか存在します。
まず、気孔や亀裂、介在物などの鋳造欠陥が生じる可能性がありますが、これらは溶湯の流動性改善や脱ガス処理、適切な冷却条件の設定、溶湯の清浄化処理などの対策で防止できます。次に、機械的特性においても検討が必要です。鋳造フランジは鍛造品と異なり流線型の内部組織を形成しないため、特定方向の強度が劣ることがありますが、熱処理や合金組成の最適化によって性能向上が可能です。さらに、精度面での課題も挙げられますが、鋳造後の機械加工プロセスを導入したり、金型鋳造技術を採用したりすることで高精度化を実現できます。
鋳造フランジと鍛造フランジの比較
フランジ製造には鋳造法以外に鍛造法も用いられており、それぞれに特徴があります
鋳造フランジの特徴
- 複雑な形状の製造が可能
- 初期投資コストが比較的低い
- 大量生産に適している
- 鋳造欠陥のリスクがある
- 内部組織が均一でない場合がある
鍛造フランジの特徴
- 高い機械的強度を持つ
- 内部組織が流線型で均一
- 欠陥が少ない
- 複雑な形状の製造が難しい
- 製造コストが高い傾向にある
他工法(旋盤・切削)との比較
特性 | 旋盤加工 | 切削加工 | 鋳造加工 |
---|---|---|---|
加工原理 | 回転する工作物に工具を当てて成形 | 固定工作物に回転/直線運動する工具を使用 | 溶融金属を型に流し込み冷却・固化 |
精度 | 高い(±0.01mm程度) | 非常に高い(±0.005mm程度) | 中~低(±0.5mm程度、後加工で向上) |
表面粗さ | 良好 | 優れている | 粗い(後加工が必要) |
生産効率 | 中(単純形状は高い) | 低~中 | 高(特に大量生産時) |
コスト | 中 | 高い | 初期コスト高、量産時は低 |
形状の複雑さ | 単純~中程度(回転対称形状) | 複雑な形状も可能 | 非常に複雑な形状も可能 |
材料ロス | 多い | 多い | 少ない |
適したサイズ | 小~中 | 小~中 | 小~大(特に大型に適している) |
材料の制約 | 少ない | 少ない | 鋳造可能な材料に限定 |
品質の一貫性 | 高い | 高い | 比較的低い(鋳造欠陥の可能性) |
設備投資 | 中程度 | 高い | 非常に高い |
熟練度の要求 | 高い | 中~高 | 高い(型設計・鋳造条件) |
後加工の必要性 | 少ない | 少ない | 多い |
旋盤加工によるフランジ製造
旋盤加工は、回転する工作物に固定された工具を当てることで、フランジの形状を削り出す加工方法です。
特徴
棒材や円盤状の素材を旋盤に取り付け、外径加工、端面加工、穴あけなどの工程を経てフランジを形成します。NC旋盤を活用することで、高精度かつ効率的な生産が可能になっています。高い寸法精度と良好な表面仕上げが特徴です。
メリット
回転対称形状の加工に最適
高い寸法精度と表面品質が得られる
少量生産から中量生産まで柔軟に対応可能
設備投資が比較的少なくて済む
デメリット
非回転対称形状の加工には不向き
大型フランジの製造には効率が悪い
材料のロスが大きい
熟練した技術者が必要
適用範囲
- 精密な寸法が要求される小~中型のフランジ
- シンプルな円形の形状を持つフランジ
- 特殊材料を使用するフランジ
- 少量~中量生産のフランジ
切削加工によるフランジ製造
切削加工は、主にマシニングセンタなどを使用して、固定された工作物に対して工具を移動させながら加工を行う方法です。
特徴
素材をマシニングセンタに固定し、複数の工具を使用して段階的に形状を削り出します。多軸制御により、複雑な形状も加工可能です。フランジの外形だけでなく、ボルト穴や溝、特殊形状も一台の機械で加工できます。
メリット
複雑な形状の加工が可能
非常に高い精度が得られる
多様な材料に対応可能
設計変更に柔軟に対応できる
デメリット
加工時間が長い
生産コストが高い
材料の無駄が多い
大型フランジの製造には不向き
適用範囲
- 複雑な形状のフランジ
- 高精度が要求されるフランジ
- 特殊なデザインや機能が必要なフランジ
- 多品種少量生産のフランジ
鋳造加工によるフランジ製造
鋳造加工は、溶融した金属を型に流し込み、冷却・固化させることでフランジ形状を作り出す方法です。
特徴
型の製作、溶解、注湯、冷却、型抜き、後処理という工程を経てフランジを製造します。鋳造方法には、砂型鋳造、金型鋳造、遠心鋳造など様々な方法があります。材料と組織については、鋳造特性の良い材料(鋳鉄、鋳鋼など)が使用され、内部組織は凝固過程で形成されます。
メリット
複雑な形状も一度の工程で形成可能
大量生産に適している
大型フランジの製造に適している
材料のロスが少ない
デメリット
鋳造欠陥(気孔、亀裂、介在物など)のリスクがある
精度が他の方法と比べて低い
後加工が必要になることが多い
初期投資(型の製作など)が高額
適用範囲
- 大型フランジ
- 複雑な内部形状を持つフランジ
- 大量生産が必要なフランジ
- 高い機械的強度よりもコスト効率が重視されるフランジ
───────────────
フランジの調達はTOHMAへお任せください
当社ではフランジをはじめとした鋳造品の調達を承っております。大型鋳造品(500⾓‧ φ300以上)の取り扱いが可能で、塗装・表面処理も一貫して対応いたします。
調達を依頼いただくことでコストややり取りが増えることを懸念される方もいらっしゃいますが、工法の見直しや製図等の生産工程の一部を弊社で負担することで、転注検討でご相談いただいたお客様の約9割が同程度の取引価格、もしくはコストダウンを実現しております。
製造業界経験10年以上の担当者がスピーディーに対応いたしますので安心してお任せください。