マニホールドブロックの調達はTOHMAへお任せください
当社ではマニホールドブロックをはじめとした鋳造部品の調達を承っております。小・中型部品だけでなく大型鋳造品(500⾓‧ φ300以上)の取り扱いも可能で、塗装・表面処理も一貫して対応いたします。
調達を依頼いただくことでコストややり取りが増えることを懸念される方もいらっしゃいますが、工法の見直しや製図等の生産工程の一部を弊社で負担することで、転注検討でご相談いただいたお客様の約9割が同程度の取引価格、もしくはコストダウンを実現しております。
製造業界経験10年以上の担当者がスピーディーに対応いたしますので安心してお任せください。
Contents
マニホールドブロックについて
マニホールドブロックは、油圧・空圧・冷却・燃料など各種流体を効率的に分配・集約するために使われる中空ブロック部品です。複雑な配管を内部流路として一体化することで、省スペース化や漏れリスクの低減、組立工数の削減といった多くの利点をもたらします。
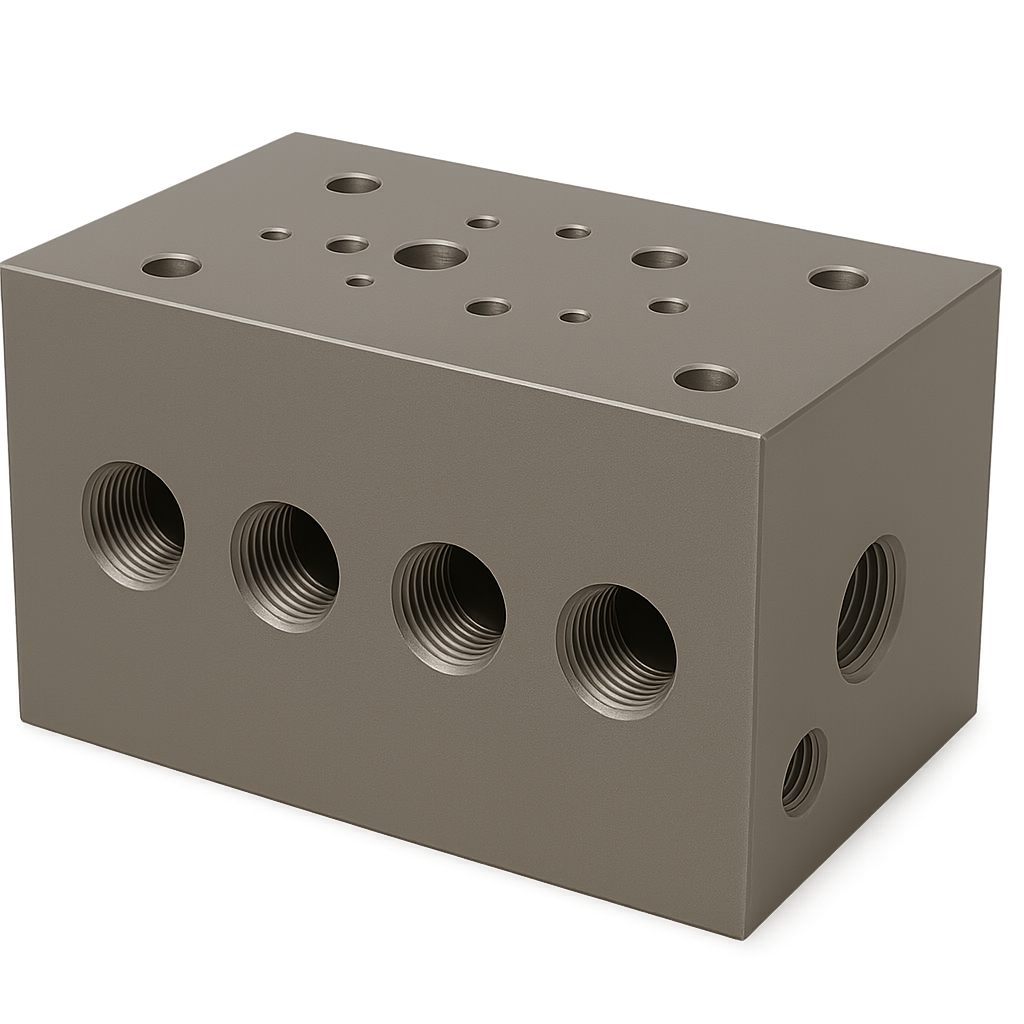
流路抵抗と流量バランスの最適化
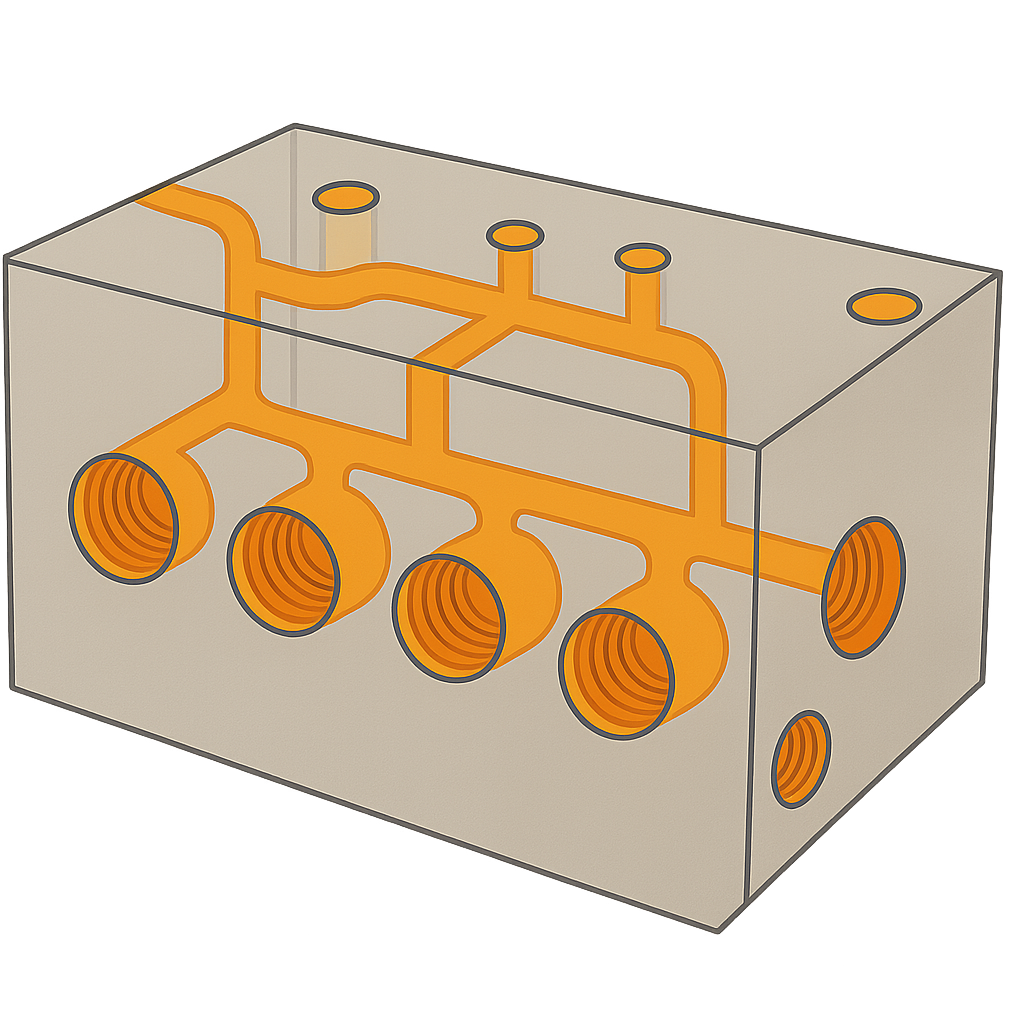
マニホールドは複数の流体経路が一箇所に集約される構造のため、流体力学的な観点から適切な設計を行わないと、流量の偏りや圧力損失が発生するリスクがあります。特に注意すべきは流路抵抗で、これは流速の2乗に比例して増加します。したがって、必要流量を確保するためには、流速を上げすぎない設計が求められます。
この対策として、主管や分岐管には十分な内径を持たせ、できる限り圧損の少ないスムーズな流路形状にします。たとえば、急激に断面が変化する箇所や鋭角に曲がる部分は局所的な抵抗源となるため、曲面で徐々に変化させる形状が有効です。また、T字分岐では一方に流れが集中しやすくなるため、入口から直線部分を長めに確保したり、流れのガイド構造を取り入れることで流量を分散させる工夫が施されます。
並列に配置された複数の枝管に均等な流体を供給する際には、各流路の圧力損失バランスが重要です。このとき、対称的な配置に加え、あえて各流路に小さな絞り(オリフィス)を設けて抵抗を調整する手法も用いられます。これにより全体として均一な流量分配が実現できます。
特にマイクロ流路や多数の並列チャンネルを持つ熱交換系では、流体解析ツールを用いた流量シミュレーションが有効であり、事前に流路ごとの流速や圧力を可視化することで、不均一な流れを未然に防ぐ設計が可能になります。
応力集中を避けた強度設計
マニホールドは内部圧力だけでなく、配管やバルブの荷重、さらには熱膨張による応力にもさらされるため、構造的に十分な強度を持たせる必要があります。ただし、単に肉厚を増やせば良いというわけではなく、重要なのは応力集中の回避です。
応力集中とは、形状上の不連続点(角部、穴の縁、段差など)に力が集中し、局所的に破壊の起点となりやすくなる現象です。これを避けるには、まずコーナー部や穴周辺に十分なR(曲面)や面取りを設けて、鋭角を作らないことが基本です。Rを大きくすればするほど応力集中係数は下がり、局所的な破損リスクを軽減できます。
また、厚みや幅が急激に変わるとその部分に力が集中するため、断面の遷移は可能な限り緩やかに設計します。例えば、板からパイプへの接続部ではテーパー形状や補強リブを使って応力を分散させるのが有効です。
さらに、溶接部はとりわけ注意が必要です。ビード形状による段差や溶接熱による硬化・残留応力は、破断や疲労の原因となり得ます。そこで、溶接後にビードを研磨して平滑化する、必要に応じて応力除去焼なまし(SR処理)を行うといった対策が有効です。
最終的な強度確認には、有限要素解析(FEA)を活用することで、部品全体の応力分布を可視化できます。局所的に応力が高まる箇所があれば、形状修正や補強設計を通じて問題を事前に潰すことができます。
シール性と漏れ対策の基本
マニホールドの最も基本的な機能は、内部に流体を安全に閉じ込めることです。そのため、シール性の確保は設計・製造のあらゆる段階で重視されなければなりません。
特に漏れのリスクが高いのが、接合部(フランジ、ねじ、溶接)です。フランジの場合、剛性や面圧を考慮した適切なガスケットの選定と、ボルト本数や締め付け力の確保が重要です。また、ガスケットの性能を最大限発揮させるには、フランジ面の粗さも所定の範囲に仕上げておく必要があります。
ねじ込み式の継手では、有効ねじ長・ねじ精度を管理し、シール材やテープを前提とした構造設計が求められます。ここでも過度な応力集中や過トルク締結による損傷がないように配慮します。
溶接構造の場合は、全周溶接や裏波溶接で十分な溶け込みを確保することが基本です。箱状の構造で隅部に死角があるような場合は、シール溶接専用の溝を設けたり、構造を見直して隙間の発生を防ぎます。また、溶接線の総延長を短くする設計も漏れリスクの低減に寄与します。できるだけ一体成形や曲げ加工で部品点数を減らし、接合部自体を少なくすることが望ましいと言えるでしょう。
加えて、使用環境に適した材料選びもシール性を維持する上で重要です。水系や油系であればステンレスや防錆処理済みの鋼材が好ましく、異種金属の接合は電食(ガルバニック腐食)による微小漏れのリスクを伴うため、避けるか防食対策を講じる必要があります。
鋳造加工のポイント
鋳造加工により製造する場合は、溶融金属を型に流し込んで一体成形します。ダイカスト(高圧鋳造)や砂型鋳造を用いて、複雑な外形や中空部を効率良く形成できます。鋳造後に必要な箇所だけを機械加工で仕上げることで、コストと工数を大幅に削減できます。
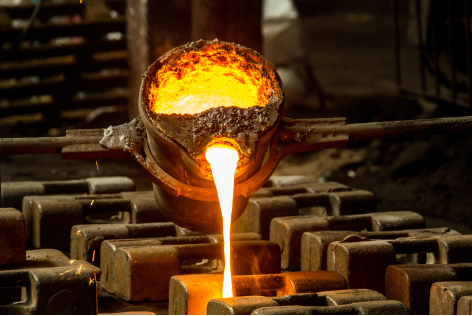
鋳造時の注意点
鋳造では「ひけ巣」や「ブローホール」といった内部欠陥が発生することがあります。これらは凝固時の体積収縮や空気の巻き込みによって生じるため、押し湯(ライザー)設計や鋳型通気性の確保、湯流れ解析の活用が欠かせません。
また、型から部品を抜くための「抜き勾配」や、内部流路を形成するための「中子(コア)」の設計も重要です。過剰な中子使用は破損や残留砂の原因となるため、後工程で機械加工する部分と鋳造で成形する部分の最適な役割分担が求められます。
欠陥対策と品質管理
鋳造品は、外見だけでは内部品質を判断しにくいため、非破壊検査(X線・超音波)や耐圧試験による品質管理が必要です。また、鋳造段階でシミュレーションソフトを使った湯流れ・凝固予測を行うことで、量産前に不良リスクを可視化できます。
機械加工におけるポイント
切削加工により製造する場合は、ブロック材からドリル・エンドミル・タップなどを使って流路やねじ穴を加工していきます。設計変更や少量多品種への対応に優れており、特に高精度が要求される場合や強度信頼性を重視する場合に選ばれます。
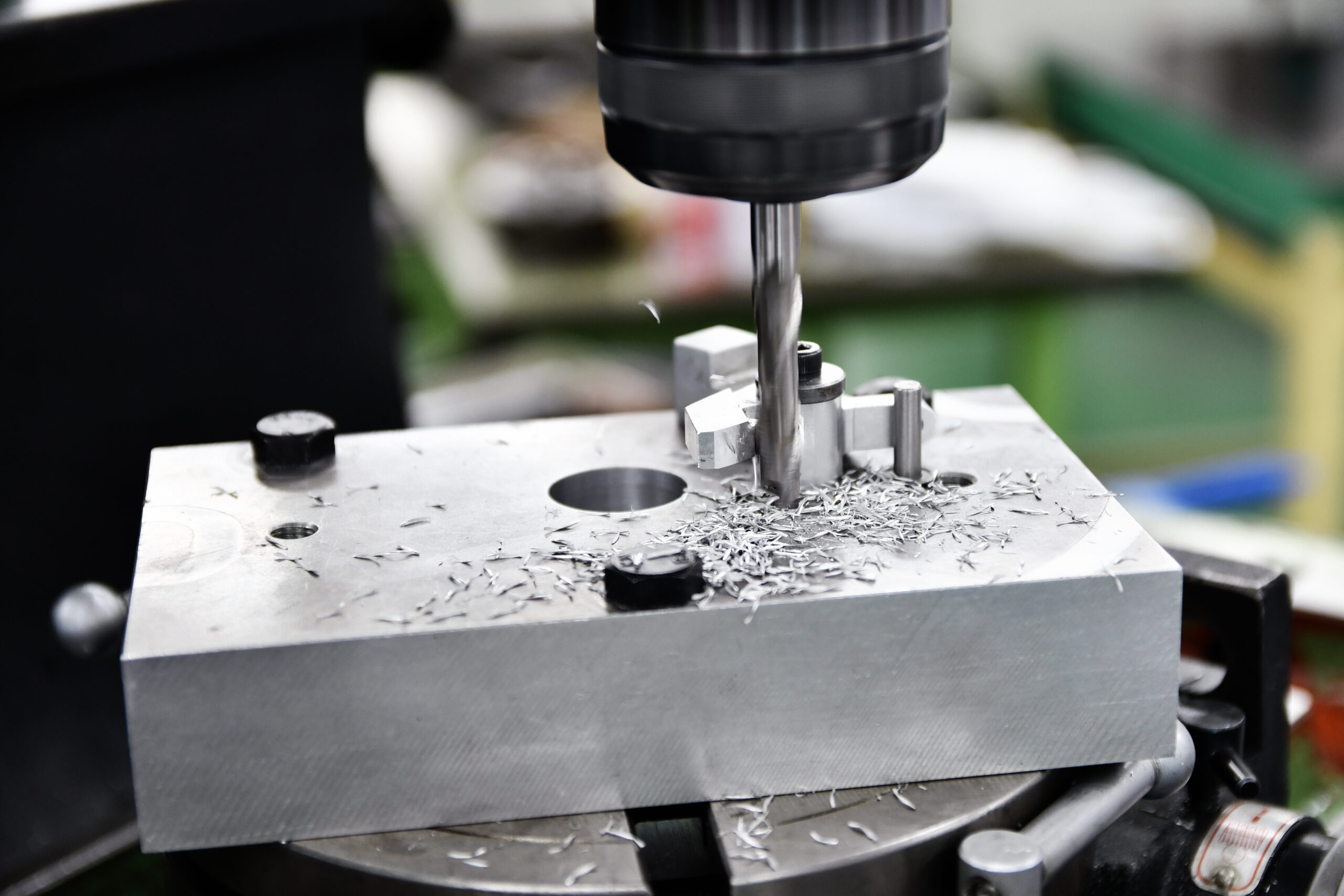
加工性を意識した設計がカギ
マニホールドの設計では、すべての内部流路が「まっすぐな穴で加工可能か」が重要です。ドリルは直線方向にしか加工できないため、流路同士を交差させる設計では、必ず交点にアクセスするための余分な穴(サービスホール)を設ける必要があります。この穴は後にプラグで塞ぎます。
また、ポート配置は加工の方向を最小限に抑えるように工夫することで、加工効率が上がり、治具設計やプログラミングの負担も軽減できます。
深穴加工とバリ処理
マニホールドには、ブロックの端から端まで貫通する深穴や、交差する穴が多く存在します。深穴加工ではドリルのたわみや位置ずれを防ぐために、段階的なドリル操作や切削油の高圧供給が重要です。
交差穴では工具のブレによってバリが発生しやすく、バリが内部に残ると、油漏れやバルブ詰まりなど重大なトラブルを引き起こします。そのため、バリ除去と内部洗浄は極めて重要な工程です。エアブローや洗浄液、場合によっては内視鏡を用いての確認が必要になることもあります。
タップ加工とシール性能
ねじ部の加工では、「穴あけ→タップ」の順序を守り、ねじ切り用の切削油を使用することで、ねじ山の品質と工具寿命を確保します。ねじ部の傷や残留切粉はシール不良の原因になるため、仕上げ後には必ずねじ部の清掃を行い、ねじゲージによる検査も行います。
製品調達事例
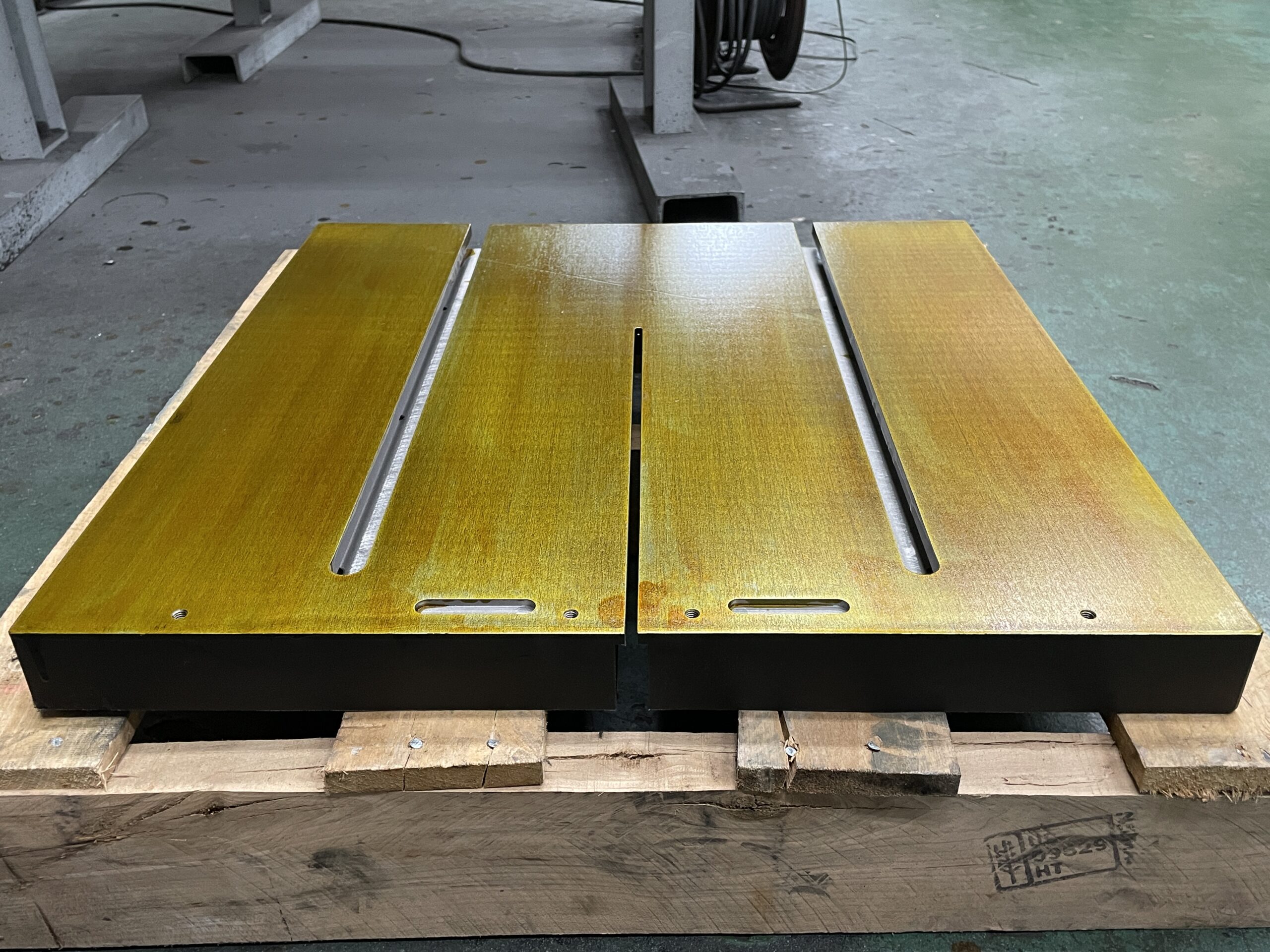
マシンテーブル
サイズ:500*500*40(W*D*H)
材質 :FC250
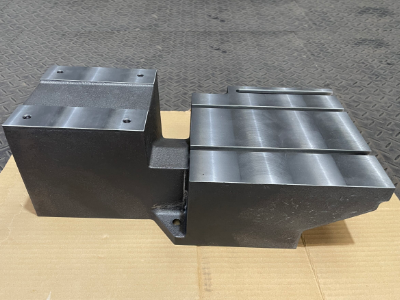
メインベース
サイズ:460*250*160(W*D*H)
材質 :FC250
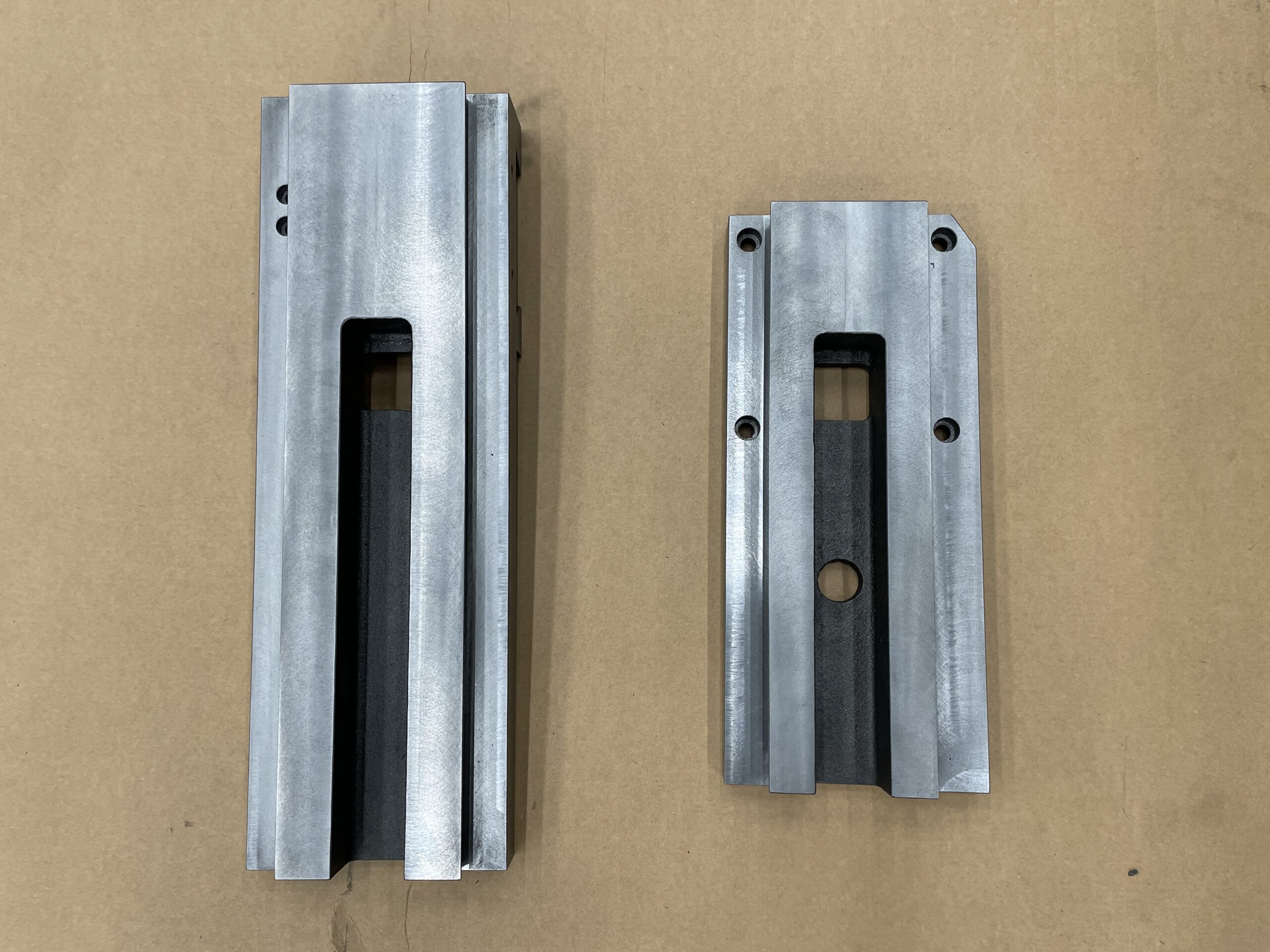
スライドユニット
サイズ:左:430*140*60(W*D*H)
右:320*140*40(W*D*H)
材質 :FC250